Human Resources Training
The Group’s employee training programs
Employee Training Programs (Japanese page only)
Overview of initiatives
(1) Training systems
Training Systems (Japanese page only)
(2) Overseas training system
Training Outside Japan (Japanese page only)
(3) New employee training
Yasuda Logistics reorganized human resources training programs, effective from July 1, 2021, as part of management system improvements and organizational restructuring under Long-term Vision for 2030.
The Company’s new personnel system:
(1) encourages awareness of good conduct among employees through an evaluation system
(2) draws on the diversity of employees and work styles
(3) improves training to develop practical skills and throughout the Company as a whole
Promoting Widespread Understanding of the Group’s Management Philosophy
For the Yasuda Logistics Group, it is essential that employees understand the Group’s aspirations and goals, and all members of the Group work together to reach those results. Therefore, to ensure that the management philosophy and policies are widely understood, the Group carries out the following measures.
Overview of initiatives
(1) Issuing the YASDA Value Book
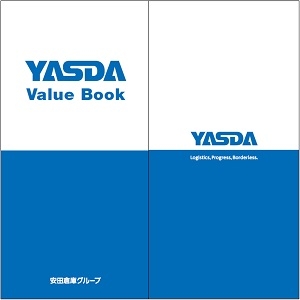
The YASDA Value Book, containing the Yasuda Logistics Group’s management philosophy, code of conduct, and management plans, is distributed to all employees to provide a source of guidance and for widespread awareness of the Group’s values, standards of behavior, and goals.
(2) Workshops on sustainability
Since July 2022, the Yasuda Logistics Group has been holding monthly workshops to raise awareness of sustainability within the Group. These workshops provide reliable information on a wide range of rapidly changing sustainability issue. As well, these workshops encourage every employee to consider how sustainability impacts the Group and to take these issues to heart. The Group intends to have employees collectively value sustainability by sharing opinions in the workshops.
Diversity and Inclusion
Overview of initiatives
(1) Promoting women’s success in the workplace
To promote diversity in the workplace, Yasuda Logistics actively recruits women. Since 2020, we have been offering a training program designed to prepare women for management positions. With the target of having women hold at least 10% of all management positions by March 31, 2026, the Company is implementing programs that make it easier for them to succeed.
(2) International employees
Yasuda Logistics’ subsidiaries outside Japan actively recruit local employees. The percentage of local employees assigned to management positions is relatively high, and the Group aims to increase this number even more, with the view of contributing to our success internationally. Staff from many countries are also regularly assigned to the Company’s departments handling overseas operations, encouraging international exchanges within the Group.
(3) Midcareer employees
Yasuda Logistics recruits midcareer employees through recruitment campaigns in the logistics industry. We also hire highly skilled people from diverse backgrounds from different industries, developing them as candidates for management positions. After joining the Company, midcareer employees are regularly provided with career development programs, including training on the skills needed for their new job.
You can view the results of our initiatives on our ESG Data page.
Creating Employee-Friendly Workplace Environments
Overview of initiatives
(1) Restructuring the workplace
The Company creates a workplace environment that enables employees to work in diverse ways that suit their individual attributes, in this way giving every employee a brighter outlook. Since establishing a committee tasked with workplace reforms in August 2018, the Company has held departmental meetings and executed action plans for reducing long work hours and increasing productivity, while aiming to increase career opportunities and motivate employees to make the most of their abilities.
(2) Encouraging employees to take childcare leave
The Company has formulated an action plan for creating diverse work conditions that make it easier for employees to balance their jobs and childcare, with a view to allowing all employees to demonstrate their strengths.
Yasuda Logistics Corporation’s action plan based on Japan’s law on childcare support (Japanese version only)
(3) Support for Japan’s white logistics campaign
White Logistics, a campaign for raising efficiency and improving work conditions in Japan’s logistics industry, was jointly initiated by three government ministries: the Ministry of Land, Infrastructure, Transport and Tourism; the Ministry of Economy, Trade and Industry; and the Ministry of Agriculture, Forestry and Fisheries. Yasuda Logistics has officially declared support for this campaign, With our commitment, we are striving to improve efficiency and productivity in logistics and truck transportation, while making it easier for all employees to do their jobs.
Support for the White Logistics Campaign (Japanese page only)
(4) Testing swap body containers
Yasuda Logistics and our subsidiary, Yasuda Transportation Co., Ltd., carried out a verification test of swap body containers in June 2021. Because these containers are standardized and interchangeable from one vehicle to another, they are expected to improve the operations of transportation companies. Specifically, using these containers can reduce overtime work by shortening wait times; enable one-day operation by having drivers switch duties at delivery points; attract more people to the industry by eliminating the burden of loading and unloading containers; and increase employee retention rates by improving work conditions.
Swap Body Container Verification Test (Japanese version only)
Japan’s First Verification Test of Swap Body Containers for Refrigerated Shipments (Japanese version only)
SLOC demonstration test conducted by seven companies from a range of industries (Japanese version only)
(5) Easing workloads by standardizing and streamlining operations
In February 2021, Yasuda Logistics established a new department for digitally transforming operations. By deploying AI and robotics, the Company intends to automate logistics operations and save on labor in response to projected labor shortages and growing demand for logistics services. The Company has been automating the transportation of heavy objects as well as more efficient picking and sorting by installing robots at several locations, including automatic vehicles and autonomous robots, with the goal of creating a sustainable logistics work environment.
For administrative work, the Company is deploying AI-powered optical character readers and robotic process automation to streamline routine tasks and boost productivity.
In February 2021, Yasuda Logistics acquired a stake in a company with patented radio frequency identification (RFID) technology to provide logistics solutions that can collaborate with innovative companies. In this way, the Company will transform logistics services and our business model in step with rapid technological advances while building a sustainable logistics ecosystem.
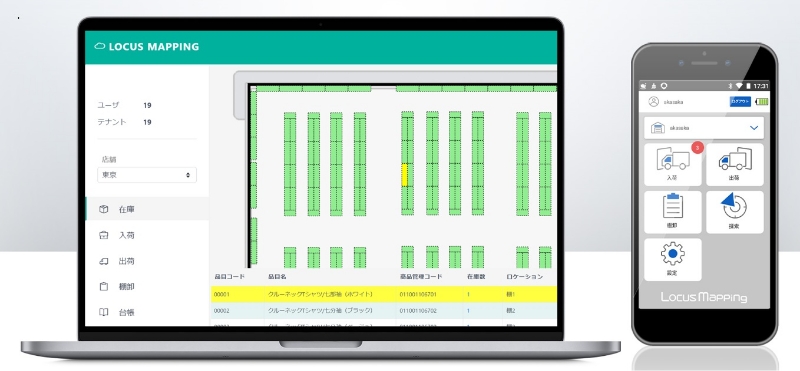
A digitized layout (left) and user interface of a handheld reader (right)
(6) Visiting every worksite to improve the work environment
Yasuda Logistics surveys conditions at all worksites and, based on the survey results, improves the environment for all employees.
(7) Promoting workplace reforms together with relocating the head office
To improve the office environment and boost the Group’s management efficiency, Yasuda Logistics along with several operating subsidiaries relocated head offices to the same building in December 2020. By having employees work together on the same floor and by adopting a desk sharing (open plan) system, the Company has created a more communicative work environment and enabled cooperation within the Group. Through these head office improvements, the Company is aiming to raise efficiency across all Group companies and worksites.
(8) Tours of workplaces for employees’ families
The Yasuda Logistics Group offers tours of offices and logistics facilities to help the family members of employees better understand our worksites. This includes business card exchanges and commemorative photos.
You can view the results of our initiatives on our ESG Data page.
Occupational Health and Safety
About the Group’s occupational health and safety
The Yasuda Logistics Group constantly strives to improve occupational health and safety from the viewpoint of being an enterprise that values people, as stated in the Corporate Code of Conduct. For this reason, we maintain safe working environments while taking steps to prevent workplace accidents and remove obstacles to good health. We also ensure the comfort and wellbeing of employees, treating all of them fairly while respecting their individuality.
Occupational health and safety system
Taking the same approach as our disaster prevention system, Yasuda Logistics has set up an occupational health and safety system led by the Occupational Health and Safety Committee that meets twice a year and is chaired by an executive officer appointed by the President. The committee members include the chairpersons of regional occupational health and safety committees as well as representatives of various Group companies. The Occupational Health and Safety Committee oversees all activities related to health and safety, and like the Disaster Prevention Committee, formulates an annual action plan at the start of each year, determines important monthly initiatives, and manages their progress.
Under the Occupational Health and Safety Committee, regional subcommittees made up of members from the occupational health and safety committees at each worksite have been set up to hold regional meetings on occupational health and safety as well as make inspections once a month. The Occupational Health and Safety Committee also conducts general inspections, whenever they are needed.
Under the direction of their respective regional occupational health and safety committees, every worksite committee makes inspections, as needed, and raises awareness of health and safety at their worksites. Similar measures are also being taken at every company of the Yasuda Logistics Group.
Overview of initiatives
(1) Limiting long work hours and encouraging employees to take paid holidays
The Yasuda Logistics Group limits long work hours and encourages employees to take paid holidays to prevent health problems caused by excessive work hours. Specifically, we ban overtime on certain days and help employees plan their days off to reduce their work hours. As well, we provide consultations with occupational physicians for employees who have worked unreasonably long hours.
(2) Promoting health management
Yasuda Logistics Group provides all employees with medical examinations and checkups for preventing lifestyle-related diseases to help them manage their health and maintain a healthy workplace. We also subsidize influenza vaccinations and proactively encourage employees to get vaccinated. In recognition of these initiatives, Yasuda Logistics received Gold Certification from the Healthy Enterprise Declaration Tokyo Promotion Council as an Excellent Corporation for Health Management.
During the COVID-19 pandemic, with the cooperation of the hospitals and clinics that administer medical exams, the Group provided COVID-19 vaccinations at worksites to quickly vaccinate employees in response to the Japanese government’s request to reduce the burden on municipalities for vaccinations.